The EC-funded CHIMERA LIFE project is a step-change in the biomass sector, as it is proposing a new waste-to-energy plant designed to burn chicken manure.
Chicken manure is a massive problem for EU because it is generating copious amounts of ammonia polluting soil, water and air. The CHIMERA project is addresing this relevant issue by means of an innovative waste-to-energy plant which perfectly fits a distributed-energy scheme, by providing district-size energy production. It is a valuable example of closed-cycle reuse and symbiosis within farmers and fertilizer’s production value-chains. CHIMERA is aiming at a circular business. By burning manure, CHIMERA will lead to remarkable economic savings for farmers, due to avoided disposal, plus electric and thermal energy produced by an ORC group included into the biomass plant.
The new CHIMERA technology
The innovative technology which is being developed by 3P Engineering, is the first one to almost fully recover nitrogen from manure and turn most of the waste into an N-P-K rich fertilizer, with few ashes and sludge as final waste to be disposed. By doing so, it will cut a huge cost for manure disposal and turn it into a possible saving/profit for every farm willing to install the plant and able to use or sell the new fertilizer.
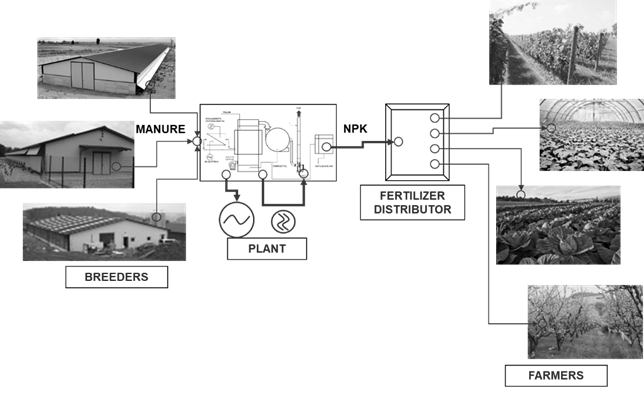
The difference between traditional process and CHIMERA technology
Manure disposal impacts heavily on GHG emissions via Ammonia and generates million tons of waste per year. Up to now, it has been a burden for farmers and a special waste. The traditional process includes: strict regulations, stock within the farm with awful smell for the neighborhood, high transport costs, need for waste treatment and reliance on external companies (e.g. for direct disposal, incinerators, biogas).
The state-of-the-art treatment relates to centralized, medium and large size plants. No plant can be reported with the expected cost-benefit balance of CHIMERA. The expected LIFE CHIMERA innovation improves the state of the art performances of biomass plants based on poultry manure and targets a future business made of smaller scale plants, delivering:
- “As-it-is” manure (no drying is required);
- Low temperature avoiding de-NOx stage;
- Sludges which are rich in N, in P, and in K, completing the formation of raw material to produce NPK fertilizer, already hydrated and ready for transformation, whereas state-of-the-art plants present very low N;
- A smaller size of plants (target 7000 tons/yy, able to produce at least 700 tons/yy of NPK fertilizer) to address different target users with a localized approach.
An in-depth overview of CHIMERA process
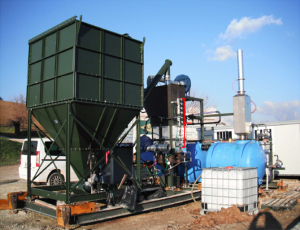
More in detail: while manure is introduced as such in the combustor (maximum allowed water content = 60%), without any preliminary drying or briquetting treatment, the burner / boiler performs a diffusive combustion of the biomass, without any tube bundle directly exposed to the biomass or to the flames or the fumes. The boiler does not provide moving parts and is inherently simpler and cheaper to build and to conduct, while ensuring a fine combustion regulation thanks to the direct intake of combustion air with precise control of internal temperatures.
The proposed system is intrinsically capable of breaking down powders (PM <50) and the flue gas treatment system is simplified: the average outlet temperature from the combustor is extremely low, with a limited emission of fine particles.
As a key to its expected success, CHIMERA allows high recovery of nitrogen paving the way to a N-P-K rich by-product to be sold or used. Its extraction comes from the fumes through the treatment water of a two-stage scrubber: in the first phase a “wet throat Venturi Scrubber” is used, suitably modified to inject water mixed with the just-produced ashes; in the second phase the fumes pass through a counter-current Scrubber before entering the atmosphere. The aqueous treatment solution is gradually concentrated on the Scrubber collecting tank in the form of sludge, which is periodically extracted and stored in suitable tanks for the subsequent chemical-physical analyzes. The sludge is then disposed of as waste characterized after having assigned its EWC. The sludge-free water is reused to continuously feed both Scrubbers; a reintegration system with external water is exclusively provided for the first start-up of the system.
The main achievements and potential future activities
CHIMERA has successfully gone through the first tests on the field and in the labs, proving the quality of the ashes and the energy output. A lean approach has kept improving the system before the realization of the first actual size prototype, to be built in the Netherlands.
Two demonstrators were under test in Italy and a final prototype will be hosted in Spring 2019 by a Dutch farmer, the family-owned company Renders & Renders, project partner.
So far, CHIMERA raised the interest of the international community and 3P Engineering was invited to present it in two main international events: the Clean Air Forum held in Paris in November 2017 and Ecomondo trade faire held in Rimini, Italy, in November 2018.
To bypass current hurdles, the project is connecting decision makers, fertilizer producers and farmers to explore all the steps needed to test this business and close the cycle between farmers and fertilizer producers. If interested in joining our External Users’ Advisory Board, please write at info@life-chimera.eu.
About
You can find more information about our project on the website www.life-chimera.eu and you can download factsheets and reports from the Documents’ section here.
Text by Elisabetta Giromini